Robot Maintenance
Learn where to get preventative maintenance for industrial robots.
Last Updated: March 6, 2023
Find robot maintenance companies now!
Finding robot maintenance can be difficult, but it is crucial for a robot's longevity and reliability. This article will focus on providing you with quality options from top companies around the United States. These companies will exceed your preventative maintenance expectations.
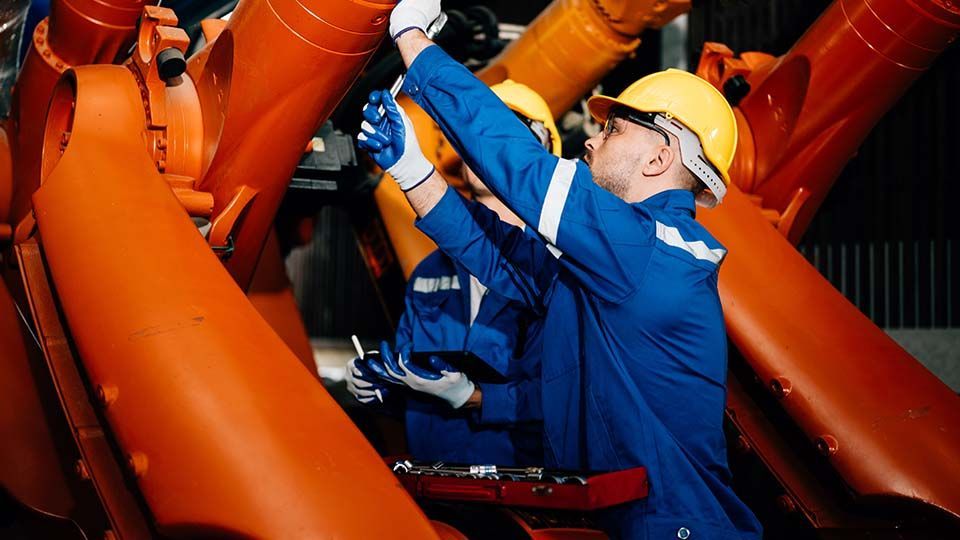
Robot preventative maintenance is vital to maintaining any automated system's well-being and helps reduce future downtime. Having a scheduled maintenance plan for your industrial robots helps ensure a much greater return on investment by increasing the longevity of the robot.
You can now find these preventative maintenance companies all in one spot. This article aims to help companies identify preventative maintenance for their industrial robots.
What is industrial robot maintenance?
Industrial robot maintenance refers to the process of maintaining and repairing industrial robots to keep them functioning at their optimal condition. This generally involves performing routine or scheduled maintenance tasks such as cleaning, lubrication, and inspection. It also includes repairing or replacing any robot components that have become worn or damaged.
Maintenance of industrial robots is critical to ensure that they operate effectively, reliably, and safely. Industrial robots can experience production delays, increased costs due to part malfunctions, and even accidents without a proper maintenance schedule.
Industrial robot maintenance can be performed by trained technicians familiar with the specific robot type. Depending on the type and robot complexity, maintenance may involve manual adjustments, software updates, or the replacement of robot components such as sensors, motors, and actuators.
How often should industrial robot preventative maintenance be performed?
To ensure proper preventative maintenance for your industrial robots, it's essential to review the maintenance manual provided by the robot manufacturer. Each robot manufacturer has a maintenance manual that outlines the recommended maintenance schedule.
For example, preventative maintenance checks should be done daily, every 1,000 and 5,000 hours of operation. Similarly, others state in the manual that daily, weekly, monthly, quarterly, biannual, and annual maintenance inspections should be completed. Following these recommended schedules by the robot manufacturers guarantees that your industrial robots receive the necessary maintenance at the appropriate times.
Regular maintenance inspections help prevent minor issues from becoming more significant problems and enable your maintenance team to work around peak production schedules. Therefore, adhering to the recommended robot maintenance schedule is essential to keep your industrial robots functioning correctly.
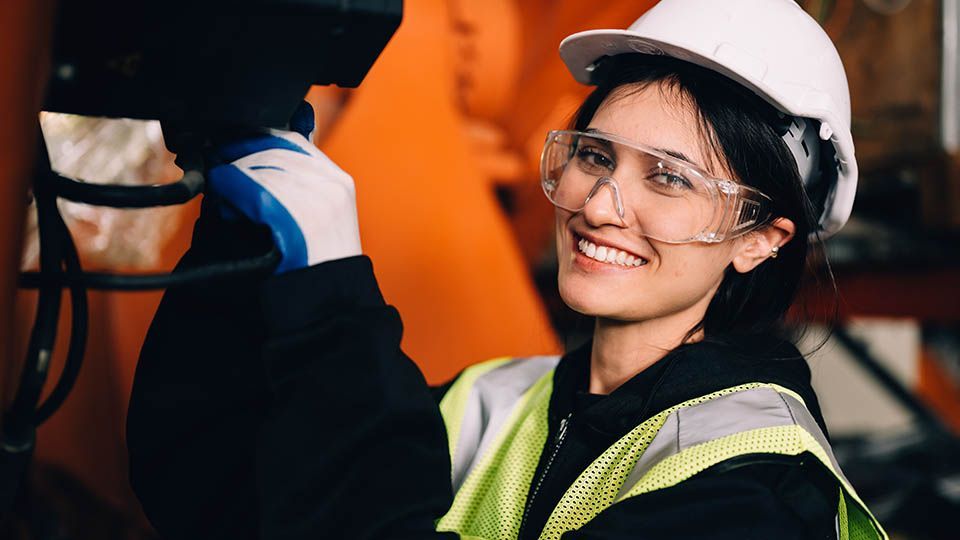
Industrial Robot Preventative Maintenance Companies:
To help you ensure your industrial robots run at peak performance, we've researched and compiled a list of the top preventative maintenance companies. These companies offer a range of services designed to keep your robots in optimal condition and minimize the risk of downtime or costly repairs.
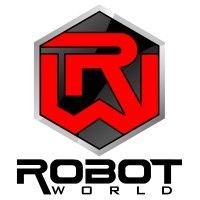
Robot Maintenance Company Highlights:
Robot Maintenance: Fanuc, Yaskawa, Universal
Site Location: Madison Heights, MI
Robot Preventative Maintenance Program Highlights:
- 28-point inspection process
- Authorized FANUC integrator
- Authorized Lincoln integrator
- Yaskawa service partner
- Universal Robots service partner
- Authorized ABB robotics value provider
- System partnership with KUKA robotics
- Equipment repair and replacement parts
Allow their team of expert robot maintenance technicians to streamline your maintenance processes. Their professional staff will create and provide a maintenance plan quote for any robot cell or standalone automated system.

Robot World hires skilled maintenance technicians with extensive experience in integration, field service, training, preventative maintenance, and technical support. They collaborate nationwide with distributors, rebuilders, maintenance personnel, and procurement professionals from all industries to assist in finding solutions for their equipment repair and replacement requirements.
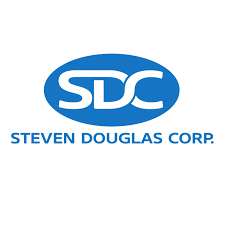
Maintenance Company Highlights:
Robot Maintenance: Automation Equipment
Site Location: Concord, OH
Preventative Maintenance Program Highlights:
- Automation machine maintenance
- Preventative maintenance plans
- Routine service
- Spare parts lists
- Machine training
- Recommended upgrades
- Operating manuals
Steven Douglas Corp. (SDC) can help a business develop a maintenance program for its automation equipment. Their team of automation experts will work with your staff to inspect, test, and clean your semi-automated and automated equipment. Their technicians will ensure your industrial machines continue to work at their peak performance.
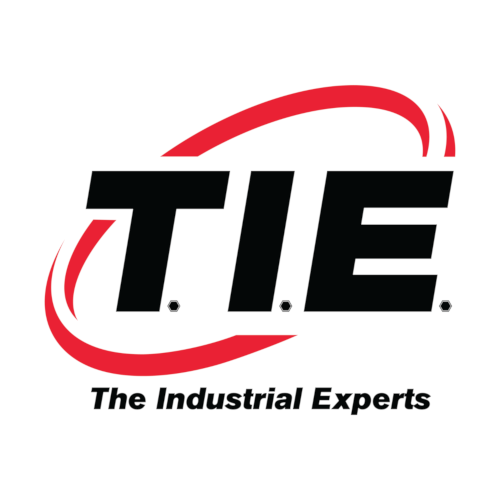
Robot Maintenance Company Highlights:
Robot Maintenance: Fanuc, ABB, Yaskawa, KUKA
Site Location: Almont, MI & La Vergne, TN
Robot Preventative Maintenance Program Highlights:
- Replacement of all backup batteries
- Replacement of controller fan filters (when applicable)
- Exterior damage inspection
- Operator panel inspection
- Teach pendant inspection
- Inspection of visible cables
- Visual check of EOAT
- Physical axis check for grease leaks & excess backlash
- Axis joint lubrication – with a check for metallic content
- Zerk fitting lubrication and cap replacement
TIE Industrial is focused on scheduling your robot maintenance before the robot breaks down, costing the company money from downtime and repair. Their thorough multi-point inspection will cover all of the high-failure components. TIE will work around your company schedule to perform robot maintenance. They will also provide a detailed report of the completed work and give an analysis, highlighting areas where future failure might occur that help suggests repairs that should be made.
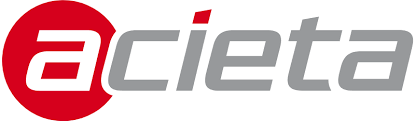
Robot Maintenance Company Highlights:
Robot Maintenance: Fanuc
Site Location: Waukesha, WI
Robot Preventative Maintenance Program Highlights:
- Fanuc authorized servicing integrator
- Robot inspections
- Grease/oil changes
- Control and vision software backups
- Controller checks
- Teach pendant checks
- General cleanings
- Certified Fanuc integrator
Acieta’s preventive maintenance plan is essential to maintaining the overall well-being of any robotic automation system. Acieta has a maintenance plan that will extend the robot's life and ensure its clients have a great return on their robot investment. They offer extensive preventative maintenance programs and have 16 master-certified service engineers available to keep the production line operational 24 hours a day.
OEM Robot Preventative Maintenance:
Get preventative robot maintenance directly from the original equipment manufacturer (OEM). Below we list the robot companies and how to get in contact with them.
Yaskawa Motoman Robot Maintenance
LEARN MORE ABOUT ROBOT MAINTENANCE:
What is an industrial robot preventative maintenance program?
A general preventative maintenance program is listed below and broken down into three main categories for an industrial robot.
Robot Controller:
- Backup robot memory
- Check the power supply
- Check cable connections
- Test batteries
- Replace filters
- Clean vents and fans
Robot Maintenance:
- Inspect brake operations
- Check seals for grease or oil leaks
- Inspect the teach pendant
- Check the overtravel limits
- Inspect the robot dress package
- Check the robot tool center point (TCP)
- Grease joints, bushings, and balancer house
Other Maintenance Services:
- Listen for vibrations or unusual noises
- Tighten all external bolts
- Oil and grease analysis
- Clean light curtains and sensors
- Safety assessment
Why is preventative maintenance necessary?
Below we list our top 5 reasons why preventive maintenance is essential for industrial robots.
- Avoiding Costly Downtime: Preventative maintenance can help detect potential problems before they cause unplanned downtime. A malfunctioning robot can cause significant delays and impact production schedules, leading to lost time and revenue.
- Increasing A Robots Lifetime: Regular maintenance can increase the robot’s lifespan, leading to a longer and more productive lifecycle. Robots may wear out prematurely without proper maintenance, leading to expensive repairs or replacements.
- Ensuring Safety: Industrial robots are powerful machines that can cause significant damage to tooling or severe injury if they malfunction. Regular maintenance can help identify potential safety hazards and prevent major or minor accidents.
- Maximization of Efficiency: Properly maintained robots can operate at maximum cycle time efficiency, reducing unnecessary energy consumption and increasing productivity.
- Warranty Compliance: Many robot manufacturers require regular maintenance to keep the manufacturer’s warranty valid. Failing to perform preventative maintenance work can void the warranty and turn into costly repairs later.
How to create an industrial robot maintenance plan?
Preventive maintenance is essential for industrial robots to operate effectively, reducing the risk of unexpected failures and prolonging the robot's life. Developing a solid robot maintenance plan that includes regular inspections and servicing can help identify potential issues before they cause significant problems. Below, we will walk you through the steps to create a practical and efficient industrial robot maintenance plan.
- Create a plan: In order for the plan to be successful; first, a detailed maintenance plan must be created. As previously discussed above, specific timeframes of the maintenance schedule should follow the robot manufacturer’s recommendations. Use the manual to create this detailed plan with the daily, weekly, monthly, and annual robot maintenance items to service.
- Implement the plan: Once the plan is created, it is time to implement the scheduled maintenance plan throughout the organization. This must include the following steps:
- Communicate the schedule to all appropriate robot personnel and staff. This includes posting the robot maintenance schedule for easy viewing in the work areas where the service will be performed. Be sure to notify personnel to ensure no production conflicts with the planned maintenance schedule.
- Train all new employees on how to properly perform maintenance tasks and perform annual maintenance training classes with experienced maintenance staff.
- Regularly review the plan: The robot maintenance plan must evolve as the robot services are performed and become more effective. It is crucial to evaluate your preventive maintenance plan. We suggest reviewing the maintenance plan at least once a year to make improvements or adjustments. This is an excellent time to review the planned outages to make sure the process has minimal impact on production or if the changes below occur:
- New automation equipment installed
- Robots are moved
- Production increases
- Robot repeatability decreases
- Increase in energy consumption
- Added shift
- Use a robot maintenance specialist: Working with third-party industrial robot maintenance specialists is often another way to stay on schedule with the plan. These technicians specialize in regular maintenance tasks and can help assess your current preventive maintenance schedule while developing a tailored plan to meet any company’s specific program. Having on-site maintenance personnel on staff may be ideal, but having the added labor can be expensive. This is why many companies work with experienced robot maintenance companies with years of knowledge of the processes and procedures of each robot type.
Benefits of robot maintenance:
Below we list our top 5 benefits that maintaining industrial robots can provide.
- Increased Reliability: Regular maintenance can help to identify and address potential issues before they lead to breakdowns or other problems. This can help ensure the robots operate reliably, reducing downtime and increasing productivity.
- Improved Performance: Regular maintenance can also help optimize industrial robot performance. Cleaning or replacing worn parts can help maintain the accuracy and speed of the robot's movements, which will positively impact its production efficiency.
- Extended Lifespan: Proper maintenance can help extend the lifespan of industrial robots by identifying and addressing issues that can lead to premature failure and malfunctions. This can maximize the return on investment in the robots and reduce the need for costly repairs or replacements.
- Increased Safety: Regular maintenance can help ensure that the robots operate safely and within their specified tolerances. This can help to reduce the risk of accidents or injuries in the workplace.
- Cost Savings: Investing in a regular maintenance plan can help to avoid costly robot repairs or replacements due to unexpected failures or unplanned downtime.
Robot Maintenance Safety:
Industrial robot safety is crucial in protecting workers from the hazards of working with powerful automation equipment. Proper safety measures can help prevent accidents, injuries, and even fatalities while ensuring that the robots operate efficiently and effectively. If you want to learn about the CDC safety guidelines, check out the safety maintenance guidelines for robotic workstations. This guide is for personnel or companies to use to help them prevent injuries and keep their employees and equipment safe.
WATCH THIS FINDING AUTOMATION CLIP
Stay Informed
Subscribe to our newsletter and get the latest automation news, trends, and topics in the industry.